Summary:
All areas designated as hazardous (Classified) locations shall be documented as required by NFPA 70, National Electrical Code, (NEC) Article 500.4. Electrical area classification (EAC) is the process of determining the existence and extent of hazardous locations in a facility containing any flammable and combustible chemicals. Some examples of hazardous chemicals and types of equipment that are reviewed include:
- Solvent sources from drums, pans, coating, spraying, and tank vents
- Leaks at pipe and hose couplings, pumps, and process instruments
- Fuel gases such as natural gas and propane
- Fuel oil tanks and pumps
- Hydrogen and propane cylinders
- Etc.
The result of the EAC process is a set of drawings that designate the physical areas in which any flammable and combustible chemicals may be present. This allows engineers and maintenance to determine the correct level of equipment safety needed to comply with NFPA 70, the National Electric Code (NEC).
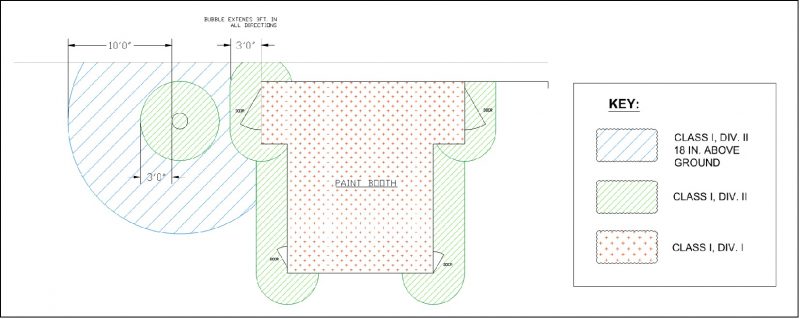
Example of an Electrical Area Classification (EAC) drawing which shows the classified regions of
a paint booth that contains hazardous solvents
How are Classified Areas determined?
EAC is usually determined by a licensed engineer working with the owner who examines the existing environment and equipment to determine regions that need to be electrically classified.
Typical Types of Rated Electrical Equipment for Classified Areas
What is the differences between Intrinsically Safe, Explosion Proof and Purge Panels that may provide electrical protection in Classified Areas?
Intrinsically safe, explosion proof and purge panels describe the most common methods of ensuring that equipment can be used in electrically classified regions.
Intrinsically Safe (IS):
Intrinsically Safe equipment is defined as “equipment and wiring which is incapable of releasing sufficient electrical or thermal energy under normal or abnormal conditions to cause ignition of a specific hazardous atmospheric mixture in its most easily ignited concentrations.” This basically means that the equipment, by design, does not have the needed power to pose an ignition threat to any nearby ignitable hazardous elements. This is common in controls and low-power passive electrical devices.
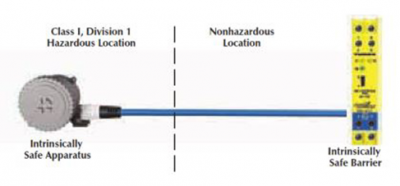
Typical Intrinsically Safe Wiring
Advantage – Cabling can be flexible
Connectors can be removed while hot
Trouble shooting while energized.
Disadvantage – Technicians need documented training
Explosion Proof (XP):
Explosion proof equipment is defined as “equipment and wiring which is designed to be sealed and rugged, such that it will not ignite a hazardous atmosphere despite any sparks or explosions within.” This differs from intrinsically safe in that there is a possibility for sparks or explosions, but that it will be contained. This is often used for equipment that requires enough power to be ignitable and is a more costly solution compared to intrinsically safe equipment.
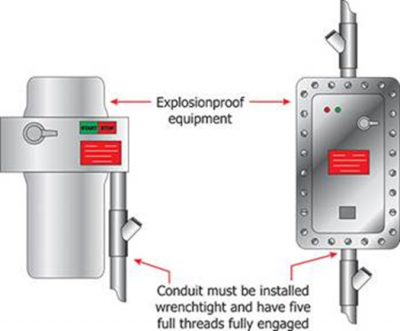
Typical Explosion Proof Enclosures and Wiring
Advantage – Less engineering design
Disadvantage – Higher maintenance requirements and cost
Purge Panel:
A purge panel is a solution for using electrical/electronic devices in hazardous areas containing flammable gases, conductive dust, corrosive gases and combination of these. In purge panels or pressurized enclosures, a fresh air source maintains a positive pressure inside the enclosure to prevent entry of outside gases in the enclosure. Prior to energizing the panel, four volumes of fresh air are required to evacuate any hazardous gases that may have accumulated in the panel/enclosure.
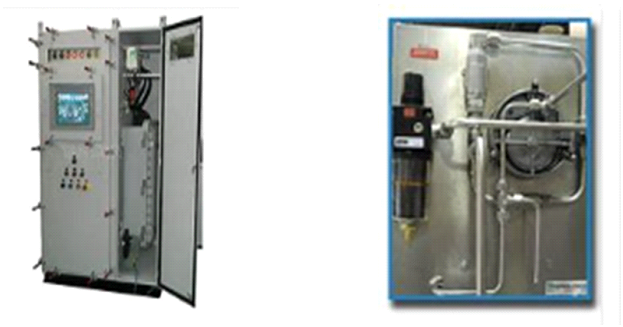
Advantage – Many more standard components
Disadvantage – Requires purging and a purge time